|
|
Introduction
Wembley was opened in 1930 as a purpose-built factory to increase the production efficiency of ordinary GLS incandescent lamps beyond what could be achieved at the GEC's original Hammersmith Lampworks. A number of building extensions were made and within a few years, at a third of a mile long, it became the largest open factory space in the world. Wembley later diversified to cover the full spectrum of incandescent and halogen lamps, and achieved numerous important developments. Its role was further expanded when Arnold Weinstock took over as Managing Director of GEC, and made Wembley the headquarters of the group's entire Lighting business. In 1990 Osram-GEC was taken over by Siemens of Germany, and it was deemed that Wembley's production was outdated and could not compete with Siemens' continental factories. This brought manufacturing to an end in 1991, and most of the site was demolished, apart from a small portion which remained as the commercial offices of Osram's UK headquarters until 1996.
|
General View of Osram Wembley Factory, taken in 1993.
|
Address |
Lumen Road, GEC Industrial Estate, East Lane, Wembley, HA9 7PG, United Kingdom. |
Location |
51.5664°N, -0.3017°E. |
Opened |
1930. |
Closed |
Manufacturing ceased 1991, with continuation of commercial activities until 1996. |
Products |
Incandescent GLS Lamps, High Wattage, Decorative Round & Candle, Reflectors, Carbon Heater, Incandescent Projection, Hardglass Halogen High Wattage, Quartz Halogen Linear, Quartz Halogen Capsule, Quartz Halogen Theatre/Studio, Quartz Infrared, Glass Bulbs & Tubing, Tungsten & Molybdenum Wire, Streetlighting Luminaires. |
Start of Operations
Osram-GEC quickly expanded to become one of the largest and most important lamp manufacturers in Britain, and by the middle of the 1920s was beginning to outgrow its original factory at Hammersmith. Partly this was due to the simultaneous increase in the requirement for electronic valves, a spinoff of the lamp industry and which were also being made at Hammersmith. In parallel, changes were being made in the organisation of how lamps were made, to achieve greater production efficiency.
Originally, lamp factories were split up into separate sections, with each being responsible for a particular process - for instance, the making of glass stems, the mounting of filaments, exhaustion and gas filling etc. Considerable effort (and hence cost) was required to transport sub-assemblies between these different departments, and continual changeovers were required to accommodate the different kinds of lamps. In order to compete in the largest segement of the market, concerning the ordinary 40W to 150W gasfilled pear-shaped incandescent lamps, it was necessary to minimise all unnecessary expenditure on labour and to streamline the production for maximum efficiency.
The architectural features of the old Hammersmith buildings were not ideal for these manufacturing arrangements, and space was becoming ever-tighter due to its location close to central London which meant that there was no room for further expansion. The decision was therefore taken to erect a purpose-built new Lampworks which would allow the labour involved in lampmaking to be slashed, and arrive at a cost-leading lamp on which the company could further grow its fortunes. It was to be located on land sufficiently far away from the centre of London to allow all possible plans for future expansion to be accommodated. The logical site for the company was at Wembley, adjacent to the Osram Glassworks which had been established in 1920, and the Hirst Research Laboratories which had also been spun out of Hammersmith a few years earlier.
Production began in 1930 in a building measuring just a third of the massive proportions that it eventually grew to occupy. As expected, the reduced cost of the lamps it was producing helped the GEC to grow rapidly, and within five years the buidling had more than trebled in length to make room for additional production lines.
|
Building Design
Fascinating details concerning the design of the new factory were published by the first Works Manager, George Chelioti, in an article entitled "The Mass Production of Incandescent Electric Lamps" which appeared in The GEC Journal, Volume 1 Issue 4, of 1931. The drawings below illustrate the general layout of production.
|
Original floorplan of Wembley factory in 1931 - the building was later trebled in length (1)
|
The first phase of the building was a three-storey construction measuring 80 feet wide by 400 feet long, with two thirds of the floor space being provided for storage. The ground floor held vast stocks of glass bulbs, this being necessary owing to the very high speed of the new Westlake type of glass bulb-blowing machines at the adjacent Wembley Glassworks which could each produce up to 100,000 per day - and which had to run making the same type of bulb for at least a few weeks in order to afford the economies of scale that were necessary for minimising costs. When required for production, bulbs of the correct type were unpacked into conveyors for automatic acid-washing followed by rinsing in near-boiling water, drying, and elevation by an electric lift to the manufacturing space above. Also provided on the ground floor were lesser stocks of all other materials, some of which were prepared for lampmaking before being raised up to the production floor - for instance the filling of metal caps with adhesive cement. Large loading doors enabled delivery lorries to be driven right into one side of the factory to the appropriate part of the store room, while a railway siding ran along the opposite side to facilitate the large volume ingress and egresss of components and finished lamps.
The top floor of the building was used for lamp manufacturing and was remarkable in that its entire area was free from any dividing walls or columns for the support of the roof. This most unusual construction is what led to the building acquiring its impressive status as the largest open manufacturing space of any factory in the world. It allowed the layout of the production machines and material transportation with complete freedom from the normal obstructions which impair the flexibility of most industrial buildings, and as a result the cost of the finished product. In the preservation of this 'sacred rectangle' of manufacturing space, all ancillary requirements such as elevators, staircases, lavatories etc. were provided as external protrusions from the main building.
Ordinarily such a vast unsupported roofspan would have resulted in a very expensive steel construction, but at Wembley this was avoided by making the roof of particularly light construction due to the elimination of its requirement to support overhead services - such as electrical cabling and gas piping. In most factories the services for each machine are tapped off from above, but Wembley took a different direction by providing these along the ceiling of the floor below the manufacturing space. The top floor was assembled from a novel cellular brick structure covered with a hardwood parquet flooring, and this permitted the simple removal of a floor cell at any location without impairing structural properties, such that gases, water and electrical services could be provided to each machine from below the floor. The resulting lack of overhead clutter gave this factory a wonderful open feeling, allowing a clear and unobstructed view from one end to the other. Furthermore the floors of all levels were novelly cambered, such that any water leakages from the machines or sprinkler system would automatically drain off to the sides rather than collecting in pools as is so often the case even in modern factories, whose floors are never perfectly flat.
The manufacture of lamps involves the detailed assembly of small parts with an extreme degree of accuracy, and high level illumination is essential. So as to avoid an increase in operational costs by resorting to the use of its own product in the provision of artificial illumination, the Wembley designers insisted on a Northlight roof combined with almost fully glazed side walls around the top floor manufacturing space. This was found to be extremely effective, the use of electric light not being required before sunset even on dull days. To facilitate continued production through the night, the original illumination scheme consisted of 750-watt GLS lamps suspended at frequent intervals 18 feet above floor level to provide a mean illuminance of 12 foot-candles. Naturally this was upgraded to a fluorescent system following the GEC's invention and later commercialisation of that more efficient light source.
On account of the endless rows of gas fires and other high temperature processes involved in lampmaking, factories for the production of this article frequently become a sweltering inferno during the summer months and this is not conducive to employee satisfaction or quality of work. These problems would normally be excerbated by providing a full-glass construction such as at Wembley. To minimise heat problems, this long and narrow building was oriented almost exactly North-South, with only the front South wall being of brick construction so as to avoid undue heating and solar glare. A high roof was also provided to allow heat to escape upards and out via novelly designed overhead vents. This might have made the building unsuitable for the wintertime production of any other product and indeed extra radiators had to be foreseen along the side walls - but a high volume lamp factory generally encounters little difficulty in keeping itself warm!
Following assembly of the lamps, the middle floor performed its function as a warehouse for finished goods, the completed lamps being conveyed downwards via gravity chutes. When required for despatch, additional chutes transported the lamps to the ground floor and onward by road and rail to the various GEC Depots around the country for final distribution to wholesalers and end consumers.
The building underwent several extensions soon after its construction, almost trebling in size within five years. Immediately prior to the second world war it was planned to double the size of the works by constructing a parallel duplicate of the main building, the two being interconnected at several bridge points to form a giant H-shaped structure. Construction on the second unit was begun, but later abandoned and what had been built was knocked down to make room for wartime air raid shelters. Later that area was converted to provide car parking space. The reason for the change of plan is believed to have been related to increasing shortages of factory labour due to the rising prosperity of Northwest London. Incidentally, the factory operated on a three-shift production system: a full 9am-5pm Day Shift, a short 6pm-10pm Twilight Shift which was mainly staffed by local married ladies, followed by a full 10pm-6am Night Shift. The dead periods between these shifts provided an opportunity for regular equipment maintenance.
Another lighting building elsewhere on the site appears to have been costructed prior to the lampworks, and was located approximately at its mid-point running transversally towards the Glassworks. Officially this was known as Building 58, or more affectionately 'Streetlighting', and later when the reality of the work there became apparent, less affectionally as 'Colditz'. This building was initially utilised for the manufacture of streetlighting lanterns. It was a 3-storey construction and when discharge luminaires requiring ballasts were introduced, these had to be carried upstairs by hand. On account of the great weight of these ballasts it soon became a less popular place to work than the adjacent lampworks, thereby earning its nickname among some employees, which was to stick right to the end. The traffic signals division of GEC later moved into this building as well. Finally, after the lighting division of the Hirst Resarch Centre (HRC) was closed and amalgamated into the Lampworks and the production of streetlighting fittings had been moved out to the Witton factory at Birmingham, Buidling 58 was employed for the measurement of lighting fittings. It housed a particularly impressively sized photometer from HRC. Commercial and design functions were also accommodated in 58, but were later split, with commercial activities relocating into the Lampworks building.
Building 56 is also of interest, sited at the far north-east of the site and adjacent to the original glassworks. This is a two-storey building, the upper floor of which housed Britain's first equipment for the automatic drawing of glass tubing, by the Danner process. After glassmaking had been decentralised from Wembley, the original glassworks was demolished but the long part of Building 56 remained and was turned over to the company's Apprentice Training Centre. It also took over the Mechanical Development Department from Hammersmith, which was responsible for the design of lamp making machinery. Life testing of incandescent lamps was originally conducted within HRC but later transferred to Building 56, before ultimately moving once again when it was integrated with the Incandescent Lamp Development Laboratory in the main building. Later still, following the closure of the main Osram lamp works, a small-scale lampmaking operation was established in Building 56 by the spinoff company Victory Lighting, who for many years continued the manufacture of some of the former special lamps produced by Osram.
|
Incandescent Developments
Being home to the company's central Research Laboratories, it is logical that Wembley became the headquarters of the entire group's Lighting business following the final vacation of the original Hammersmith works. Many new lamps were developed at the Incandescent Lamp Development Laboratory, and the adjacent Wembley lamp works benefitted tremendously from translating these experimental new models into mass-produced designs. In keeping with its founding principles to be the most cost-effective manufacturer of GLS lamps, Wembley was responsible for numerous improvements which the rest of industry then followed, for instance:
|
|
Simplification of the GLS range to utilise standard sized bulbs and internal constructions |
|
Reduction in the quantity of filament supports required |
|
Reduction in the size of bulb envelope for GLS lamps |
|
Introduction of aluminium caps to replace brass |
Additionally, a number of technical breakthroughs were made which brought a resulting increase in lamp performance and safety. Perhaps the most significant of these was the introduction of the coiled-coil filament lamp in 1934, a full two years before the American date of 1936 which is more commonly and erroneously referenced. Although coiled-coils had been produced in the 1920s, there were a number of difficulties that prevented their implementation in production. Firstly, they were much more susceptible to filament sag during life, this destroying the perfection of the originally coiled dimensions and leading to the formation of hot-spots and premature failure. Additionally, due to the shorter spacing between the filament tails, lamps having coiled-coil filaments were more likely to arc at end of life and fail explosively. Thirdly, it took many years to develop automatic machinery which could effectively handle these delicate new filaments, and allow the resulting lamps to compete in terms of cost with the earlier single coil types. These problems were all solved in Britain, and resulted in that country manufacturing coiled-coil GLS lamps two years before the design was adopted by overseas competitors.
Another Wembley development of significance was the miniature encapsulated filled fuse for incorporation in lamp stems - also known as the ballotini fuse, and within GEC as the Minarc fuse. This greatly improved the fusing behaviour, quenching end-of-life arcs inside GLS lamps more quickly and effectively than ever before. Although the ballotini fuse was a little more expensive than the standard glass-sleeved fuse, it brought a cost saving to the finished lamp because only one was needed, whereas until that time it was standard practice to include two fuses in each lamp.
By the latter part of the 1950s, the remaining incandescent production had also been delocalised from Hammersmith, so as to allow that factory to concentrate on the manufacture of electronic valves. The low wattage vacuum GLS and Pygmy types were transferred to Shaw, while high wattage GLS and miniature lamps were relocated to a new factory at Team Valley. It is believed that the balance of the Hammersmith production, concerning special lamps and photographic / projection types were transferred to Wembley. Following this, some of the projection lamps as well as the production of their filaments made a brief departure to Shaw, before once again returning back to Wembley. Certain special filaments were relocated first to the GEC's Cathode Ray Tube factory at Perivale, but also ultimately joined the Wembley wire & filaments operation.
|
Tungsten Halogen Developments
The Wembley research laboratories played a pioneering role in the development of Tungsten Halogen light sources, and in 1961 manufactured the first lamp of this type in Europe. It was a 6.6A 200W model intended for airfield lighting, and to enable a simple upgrade from the existing incandescent types it employed a miniature double-ended quartz halogen capsule sealed within the conventional glass outer envelope of the incandescent lamp. It was first used at Luton Airport.
Other developments from Wembley were equally momentous and sought to address the limitations of the original tungsten halogen lamps, which were available only in the form of a linear quartz tube pinched closed at both ends and containing an axial filament. While this arrangement was perfectly suitable for large area floodlights, they lacked the point-like nature of conventional incandescent lamps. Additionally, the manufacturing process required the fabrication of two glass-to-metal seals, which were rather difficult and expensive to form at this time.
In 1961 the work of J.A. Moore of the Hirst Research Laboratories of GEC Wembley was published, in which H.G. Jenkins presented the company's invention of the Single Ended Low Voltage halogen lamp. By pinching both tails of the filament into one single seal the construction was greatly simplified, and the introduction of a low voltage filament made the lamp remarkably compact. The world's first lamp made according to this design was the type A1/215 (FCR). It is a 12V 100W capsule having a flat mandrel filament, intended for slide projection applications. The company proposed its design to the UK projector manufacturers such as Aldis, but astonishingly they showed little interest. To achieve some commercial success, GEC therefore focussed on the retrofit market by supplying the new lamps with small adaptors enabling the replacement of conventional incandescent projector lamps. It is regrettable that the British projector manufacturers did not show more enthusiasm in the important development of the single ended halogen lamp, to allow GEC to earn the commercial results it deserved from this invention. Instead its competitor Thorn Lighting went on to win the spoils of this design, thanks to its better contacts with the considerably more innovative European projector manufacturers. GEC achieve a position of leadership in other markets, such as the use of these capsules in airfield and automotive lighting. Many capsules were produced for automive headlamps, but the company later decided to withdraw from the vehicle lighting business so as to concentrate its limited resources on discharge lamp developments. As such its total business in low voltage single ended halogen capsules never reached that of its rival, Thorn Lighting.
The company was also quick to exploit the potential for halogen technology to replace the high wattage incandescent lamps from about 500W to 10,000W, which Wembley was producing for studio and theatre lighting applications. At the time of these developments in the 1960s it was not easy to manufacture or obtain quartz tubing, which was needed for the halogen lamp owing to its high chemical purity and low moisture content. Quartz prices were high even for small pieces, and the optical quality was impaired by the presence of airlines and other surface defects. The manufacture of high wattage lamps required such large diameter and expensive pieces of quartz that it made them almost uneconomical, or leaving only a small profit margin for the manufacturer. Following the news that the group of Schilling at the German Osram company had successfully made halogen lamps using hard glass instead of quartz, and Sylvania in the USA had achieved similar success for low wattage automotive lamps, GEC jumped on this concept and ably exploited its strengths in glass science to further the concept in the direction of high wattage studio lamps.
Hardglass halogen lamps are based on the Aluminosilicate family of glasses, these having been first developed at Wembley some decades earlier to enable the creation of the world's first practical high pressure mercury lamps. The company was therefore in a prime position to extend the use of hard glasses to tungsten halogen lamps. Although the softening temperature of these glasses is much higher than traditional borosilicate hard glasses, it is not as high as quartz, and allows lamps to be made according to fairly standard processes. This important development allowed the GEC along with the independent Osram of Germany to offer halogen studio lamps at much lower prices than competitors who were forced to follow the quartz route, and gave them an early head-start in this business. Once again though, just like for the small single ended capsules, GEC was most unfortunately not to be the ultimate winner in the high wattage halogen market.
The resulting performance of the hardglass halogen studio lamps, although considerably better than incandescent in terms of lifetime and efficacy, was not quite so high as for quartz halogen designs. The lower softening point of aluminosilicate glass vs quartz meant that larger size bulb envelopes were necessary. Since these are mechanically weaker than small quartz bulbs they cannot be filled to such high gas pressures, and it is an unfortunate facet of incandescent lamp science that the lamp having the highest pressure gas fill is the more efficient and/or longest lived. For this reason, quartz lamps often show better performance than hardglass halogen.
As glassmakers began to get better and better at making quartz, its price dropped sharply and soon the small-size quartz bulbs were able to match the costs of the GEC's large hardglass versions and relatively expensive lampmaking processes, such as, for instance, the fabrication of the special glass-to-metal seals that were required. Although GEC had initially won the high wattage halogen race because it had the cheaper lamp, from the 1980s onwards it began to fall behind because it gradually lost its cost advantage and it was also behind the quartz lamps in terms of performance.
Efforts were refocussed on quartz halogen lamps, and the Wembley engineers made considerable progress not only in lamp design, but also in production processes. The company's mechanical development group was quick to develop a rotary exhaust machine for quartz capsules, and later for linear lamps, successfully beating its European rivals with this important achievement that helped reduce production costs. Despite the technical innovations, the company had lost commercial ground in halogen products, and its competitors, above all Thorn Lighting, had already acquired the reputation of having the better product.
The writing was soon on the wall that in addition to its relatively small volumes for the low wattage quartz halogen lamps, the company was also falling behind in the high wattage domain. In short, there was no clear area in which it was still an industry leader in a major portion of the halogen market. Being high value lamps on which it was possible to earn good margins, this was a most unfortunate weakness.
|
Glass Production
The GEC's original glassmaking operations were located at Lemington-on-Tyne in the North-East of England - a considerable distance away from the lamp factory at Hammersmith that required this raw material. Bulbs for electric lamps were originally blown into moulds by hand, but this situation changed radically following the development of the fully automatic Westlake Machine by the Libbey Glass Co. of USA. That machine was developed during the years 1916-1918 and was capable of automatically blowing 100,000 lamp bulbs per day. General Electric of the USA was first to recognise its importance, and took a licence to build copies of this machine for its American lampworks' in 1918. In 1919, GEC and its competitor BTH in the UK acquired a similar license.
Rather than build its first Westlake machines at the opposite end of the country, GEC erected a new Glassworks close to its Hammersmith Lampworks. Hammersmith was at the time completely full, and the central London site offered no possibilities for expansion. Wembley provided an eminently suitable location - being close enough to Hammersmith to provide good transport links, but far enough from the City to allow almost unlimited future expansion along with a source of lower cost labour. In 1920, the first glass production was established in Wembley, a decade before the first lamps were made on the site.
The Westlake machine's impressive speed was quickly doubled by the so-called Ivanhoe machine which increased production by blowing two bulbs at each machine position. It is not known if Wembley also operated Ivanhoe machines, but it was certainly upgraded to the still more efficient Ohio machines, blowing four bulbs at each machine position.
The Libbey company's excellence in the design of automatic glassworking processes was not restricted to blown ware, and in 1917 Edward Danner of that company developed an extremely elegant process for the quantity production of glass tubing. Wembley Glassworks holds special significance as being Britain's first site for the production of machine-drawn glass tubing according to the Danner Process, the standard technique still employed by most glass tubing plants around the world. It soon became the company's principal site for the mass-production of soft glass bulbs and tubing for ordinary GLS and fluorescent lamps, while the GEC's original glassworks at Lemington focussed on the production of special pot-melted glass articles and pressed ware. Wembley grew to very substantial proportions, in 1956 running a total of seven glassmaking furnaces.
Even with such vast production volumes, which hopelessly outran the rest of the lampmaking process, there was still scope for further cost reductions by speed increases. Following the development of the Corning Ribbon Machine in the USA, which can achieve blowing speeds as high as 2000 bulbs per minute, it was realised by BTH and GEC that Britain must also adopt the same manufacturing process. The cost of the new machinery as well as its output was higher than either company could justify on its own, and in 1948 the two competitors formed a joint company, Glass Bulbs Ltd., to establish the production of Ribbon bulbs in Britain. Great space was called for in the running of the ribbon machines, and it would not have been practical to install these in the GEC's existing glass works' at Wembley or Lemington, or at the BTH glass works at Chesterfield. Work started on a new purpose-built factory at Harworth in 1949, and a year later the first bulbs were blown. As the new processes were ramped up and their costs dramatically undercut the old-style bulbs, the demand for Wembley glass began to fall off. By 1959 it could no longer be justified and the production of glass components came to a close on the site.
|
Metal Production
The company's original manufacture of tungsten, moldybenum and later dumet wire was established on the top floor of the Hammersmith lampworks. Later this was transferred to Wembley, the exact date being unknown but it may be concluded from the company's catalogues, which provide details on the activities at each factory, that the Hammersmith metal production had ceased between 1956 and 1959.
Leading-in wires were also originally produced at Hammersmith, these making the transition to Wembley prior to 1951, and the Hammersmith wire welding operations having ceased prior to 1954.
In a model similar to that of the pooling of the glassworking and capmaking operations operations of GEC and the BTH/AEI group, a similar step was taken for the production of metal wires in 1961. This led to the formation of the new company "Lamp Metals Ltd.". In 1968 to attain better economies of scale, all metal production was concentrated at a single new factory on the Team Valley Trading Estate at Gateshead in the North of England, just a short distance away from the nearby Osram Team Valley Lampworks. This relocation brought metals production at Wembley to a close, and from that point onwards the site was responsible only for the final assembly of lamps using components drawn from other factories around the country. Although the ballotini-filled fuses were first applied in Wembley incandescent lamps, these were only ever produced at Team Valley.
|
The Research Laboratories
To fuel the company's growth its first chairman, Hugo Hirst, recognised that investment in lamp research and continual manufacturing improvements would be essential. Prior to the 1914 war it had relied entirely on German science and technology, the withdrawal of which was a significant blow to the company. Hirst resolved never again to let his company rely on foreign technology, and set about forming his own research laboratories - not only to provide support to the lampworks at Hammersmith and the Glassworks at Lemington, but for all of the company's other electrical divisions as well.
He recruited Sir Clifford Paterson who had previously been in charge of the light measurement section of the UK National Physical Laboratory at Teddington, and in 1919 the initial laboratories were set up within a wooden hut at the Hammersmith lampworks which had been hastily erected during the war to provide extra space for making valves. It was never the intention that the laboratories should share factory space and their establishment within the works was only for reasons of speed, to allow research to begin immediately while the new site was being designed and built. That was completed in 1922 with the relocation to a new greenfield site originally intended for housing, alongside the new Osram Glassworks on East Lane, Wembley. It formed Britain's first dedicated industrial research laboratory, and was in 1961 re-named The Hirst Research Centre.
Many of the new lighting-related concepts devised here were swiflty implemented in production and for decades to come it ensured that the GEC lampworks were kept brimming with new developments - especially in the field of fluorescent and discharge lamps, as well as the allied field of radio valves and cathode ray tubes.
In the mid-1950s, it was recognised that lamp development could be carried out the most efficiently in close proximity to the production sites, and separate Lamp Development Laboratories were established within the production sites at Wembley for Incandescent and Halogen lamps, and at Shaw for Discharge lamps. Thereafter HRC focussed on more fundamental challenges, until around 1976 when its remaining responsibilities in lamp research were transferred to the production sites.
|
Takeover by German Osram and Closure
The GEC's entire tungsten lampmaking origins can be traced back to the 1907 decision to form a joint company in London, owned equally by the GEC and one of the leading German lampmakers, the Auergesellschaft, which had invented a particularly effective method of manufacturing tungsten lamps. The Osram brand name, at first used only to identify a particular kind of tungsten lamp of the design conceived by Auer, was sufficiently powerful that the GEC soon adopted it as the name for its entire lighting division. Some years later the same move was taken in Germany when the Auergesellschaft merged with the lamp divisions of Siemens and the Algemeien Elektrizitäts Gesellschaft (AEG) to form the giant German combine, the Osram Kommanditgesellschaft (KG).
There were thus two different companies manufacturing Osram-brand electric lamps right from the outset, a situation which was tolerable on account of the fact that Osram KG of Germany owned a 50% stake in the British Osram-GEC. This situation was not destined to last however, owing to the outbreak of the first world war, following which the assets of German enterprises were seized by foreign governments around the world. In 1916 Hugo Hirst was able to buy out the former German share of Osram KG from the Custodian of Enemy Property for £260,000 - a momentous step which put the British and all overseas territories of that country under the control of the GEC. A similar situation was played out in many other countries of the world, and the loss of its factories as well as the rights to its brand name proved catastrophic for the fortunes of the original German Osram company.
Stripped of most of its prosperous export businesses, it took many decades for Osram KG to recover to the extent that it could finance the buying-back of its lost brand and businesses around the world - only to have them confiscated yet again following the outbreak of the second world war! This monumental setback for the company took many more years of slow growth from its home market to recover from, and the second buy-back operations did not begin until 1962 when Osram KG was able to recover its former brand and factories in France, followed steadily by many of its other overseas territories.
Years of intense negotiations followed between Osram KG and GEC, but the directors of GEC made it clear that they would not entertain any ideas of selling any share of their immensely profitable Lighting division back to the Germans. Eventually in 1967 the Germans came to the realisation that if they wanted to get back into the lighting market of Britain and its colonies around the globe, they were going to have to do so by building the business up again from scratch - and in competition against the formidable GEC. As such they formed the new company 'Wotan Lamps Ltd.' in Britain and many other countries around the world - the change of name back to this former Siemens brand being necessary because Osram KG had lost its rights to the Osram trademark following the confiscations during the war.
As the years went on, and particularly in the decades following the leadership of the GEC under Sir Arnold Weinstock, the mentality did began to change, and GEC became more interested in other electrical avenues. It had been under-investing in lamps and losing market share to its rivals, Thorn Lighting and Philips, and it must have been becoming clear that the Osram-GEC lighting division was simply too small to compete in the increasingly globalised markets. A decision was reached on 19th March 1986 whereby German Osram (in the mean time becoming Osram GmbH) aquired 49% of Osram-GEC - and thereby regained control of its brand name in Britain and the remaining countries of the world, which it had lost an incredible 72 years earlier! So momentous was the occasion that a large rock was placed outside the company's headquarters in Munich, specially engraved to mark the historic re-acquisition of the last of its former divisions which had been lost following two world wars. The shareholding was increased to 100% in 1990, when GEC finally made the decision to exit the lighting business.
The Wembley factory had enjoyed six decades of production as the GEC's principal lamp works, and this change of ownership was to have a profound impact on its future. Osram GmbH had exploited its strengths in halogen lamps to put it in a considerably stronger position than Wembley, both in its manufacturing competence as well as the wide range of advanced new products it had brought to the market. Its incandescent manufacturing operations had also not stood still, as had been the case at Wembley following the years of under-investment in further production mechanisation, and it had GLS machinery running at speeds of 5000 per hour, some 30% swifter than Wembley had achieved and with a consequent saving in production costs. The British operations were unable to meet the targets necessary to allow it to compete with the GmbH's continental facilities, and this most regrettably led to the closure of production in 1991. Osram's UK headquarters remained in the front half of the building, and the rear production area was demolished in 1995. In 1996 the Headquarters moved out to a new building, and in 1999 the remainder of the building was demolished.
|
Victory Lighting
A small part of the Wembley operations continue to live on, under the name of Victory Lighting Ltd. Osram had certain governmental contracts for the supply of special lamps made at Wembley, and it would have been troublesome to keep those types in production by transferring them out to other factories. A solution was found by establishing a small factory for special incandescent and halogen lamps on the opposite corner of the GEC estate, in Building 56 of the former Glassworks and Apprentice Training building. Victory Lighting operated independently and sold these special lamps back to Osram. In 1994 Victory grew following the closure of the Thorn incandescent factory at Kent Street, Preston, from which it also took over the production of several special incandescent lamps.
The company has become particularly innovative in the manufacture of quartz halogen infrared lamps, and has since grown to be one of the principal global forces specialised in the development and production of that heat source. Lampmaking continued under Victory at the Wembley estate until 2003, when it was finally necessary to transfer the lampmaking again owing to the high costs of labour in Britain.
|
Polaron Lamps
Another small part of the Wembley operations was rescued with the formation of Polaron Components Ltd. Perhaps owing to the formation of the Hirst Research Centre by the head of the light measurement section of the UK's National Physical Laboratory, a close link was maintained between those two sites and HRC continued scientific research in the directions of light measurement. Although immensely precise equipment had already been developed for the measurement of light, the accuracy of those measurements depends entirely on the quality of the calibration of the equipment. Whereas the principal countries of the world retain various reference standards for the basic units of mass, length, and so on, it is somewhat more difficult to maintain a standard for the basic unit of light. Naturally, the original reference source was the Candle, and the output of lamps was rated in terms of candle power - however the actual luminous flux emitted by a candle is of course dependent upon its materials, construction and burning conditions, making it a particularly unreliable source. Efforts were later made to create an improved constant light source around a precision kerosene flame, but this also suffered too many variables. Similarly, ordinary electric lamps are unreliable reference sources because their luminous flux changes slightly as a function of lifetime, operating position etc, and parasitic surface reflections from the glass bulb can easily deliver erroneous measurement results.
HRC developed a number of incandescent lamps having special constructions to limit these variables and provide light sources having impressive stability, as well as in special constructions which facilitated their measurement in photometric equipment. Many of these designs went on to be employed as the world standards for light measurement - and the closure of Wembley would have left an important gap in our ability to measure light. Even though the quantities required are just a handful of lamps per year, the selling prices for these precision-instruments are sufficiently high that it was possible to maintain their production, which was taken over by the Polaron division of Cooper Controls.
|
Photographs
|
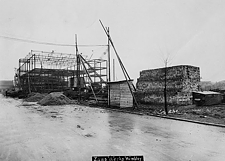 |
|
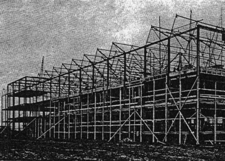 |
|
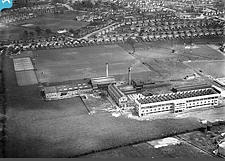 |
|
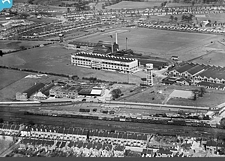 |
Factory During Construction, Rear (11) |
|
Factory During Construction, Front (1) |
|
Aerial View, 1930 (12) |
|
Aerial View, 1932 (12) |
|
 |
|
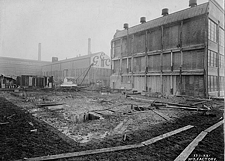 |
|
 |
|
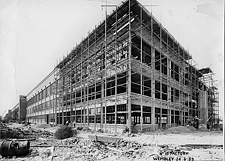 |
View from South West, 1932 (13) |
|
1933 Extension, Colditz, Glassworks(11) |
|
View after First Extension, 1933 (11) |
|
Final Rear Extention, 1935 (12) |
|
 |
|
 |
|
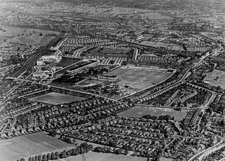 |
|
 |
View from Rear, after 1935 (11) |
|
View from South East, 1937 (14) |
|
Aerial View, c.1939 (11) |
|
Painted in Wartime Camouflage(11) |
|
 |
|
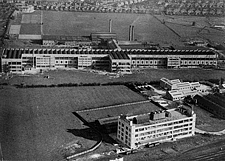 |
|
 |
|
 |
View from South West, 1952 (3) |
|
Aerial View, 1953 (11) |
|
Front Entrance, 1965(11) |
|
Front Entrance, early 1980s(19) |
|
 |
|
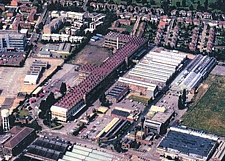 |
|
 |
|
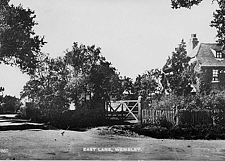 |
Front Entrance, 1994 |
|
Aerial View of GEC Estate, 1990 (12) |
|
Demolition of Main Factory, 1996(11) |
|
View from East Lane, 1860 (12) |
|
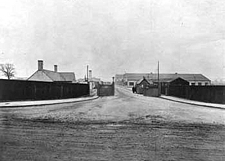 |
|
 |
|
 |
|
 |
View from East Lane, 1933 (11) |
|
View from East Lane, 1952 (3) |
|
View from East Lane, 1951-56 (11) |
|
View from East Lane, 1999 (11) |
|
 |
|
 |
|
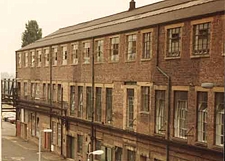 |
|
 |
View from Lampworks to Bldg. 58 (11) |
|
Front View of Building 58 (Colditz) (11) |
|
Side View of Building 58 (Colditz) (11) |
|
Rear View of Building 56 (Victory) (11) |
|
 |
|
| |
|
|
|
Side View of Building 56 (Victory) (11) |
|
|
|
|
|
|
Photographs - Lampworks
|
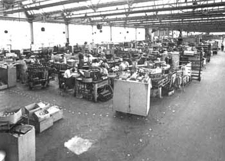 |
|
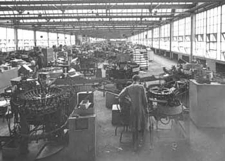 |
|
 |
|
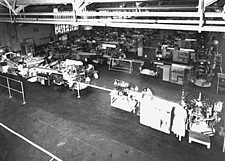 |
General View of Lampworks, 1950s (11) |
|
General View of Lampworks, 1950s (11) |
|
General View of Lampworks, 1965 (12) |
|
General View of Lampworks, 1965 (11) |
|
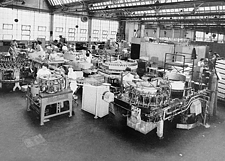 |
|
 |
|
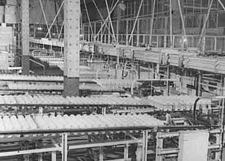 |
|
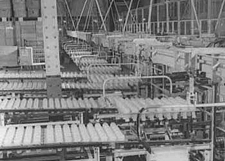 |
Typical GLS Line, 1952 (3) |
|
Typical GLS Line, 1958 (4) |
|
Bulb Washing System, 1950s (11) |
|
Bulb Washing System, 1950s (11) |
|
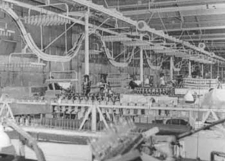 |
|
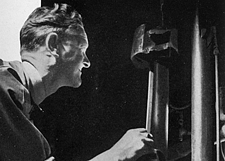 |
|
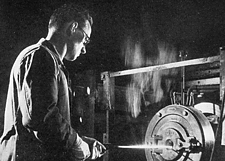 |
|
 |
Bulb Distribution to Lines, 1950s (11) |
|
Sintering of Tungsten Bars, 1952 (3) |
|
Swaging of Tungsten Bars, 1952 (3) |
|
Anstee Filament Coiling m/c, 1952 (3) |
|
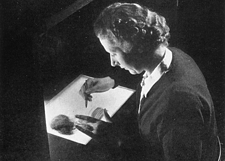 |
|
 |
|
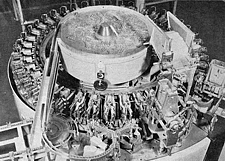 |
|
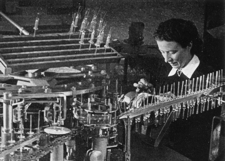 |
Coiled Filament Inspection, 1952 (3) |
|
GLS Stem / Pinch Machine, 1963 (6) |
|
Continuous Motion Stem m/c, 1963 (6) |
|
GLS Stem - Mount Transfer, 1952 (3) |
|
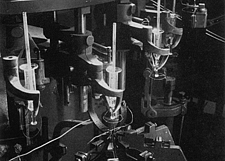 |
|
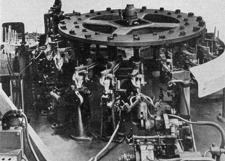 |
|
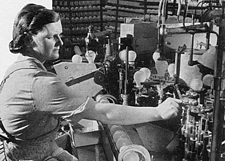 |
|
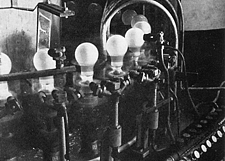 |
GLS Filament Mounting, 1952 (3) |
|
GLS Filament Mounting, 1963 (6) |
|
GLS Sealex Machine, 1952 (3) |
|
GLS Sealing Detail, 1952 (3) |
|
 |
|
 |
|
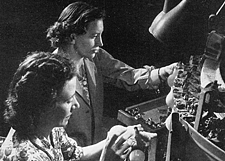 |
|
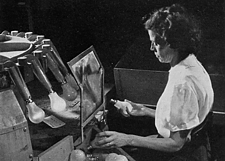 |
GLS Sealex Machine, 1958 (4) |
|
GLS Sealex Machine, 1963 (6) |
|
GLS Capping Machine, 1952 (3) |
|
GLS Ageing Machine, 1952 (3) |
|
 |
|
 |
|
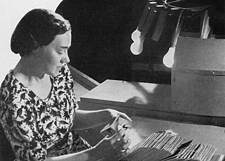 |
|
 |
GLS Cap & Ageing Machine, 1958 (4) |
|
GLS Cap & Ageing Machine, 1963 (6) |
|
GLS Hand Packaging, 1952 (3) |
|
GLS Inspection, 1952 (3) |
|
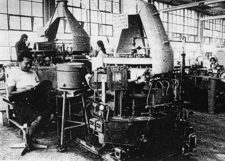 |
|
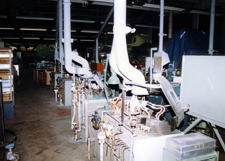 |
|
|
|
|
Auto Halogen Capsule Line, 1974 (4) |
|
Row of Mk4 Quartz Pinch Machines (11) |
|
|
|
|
Photographs - Glassworks
|
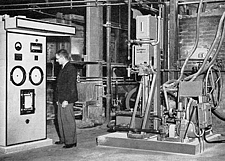 |
|
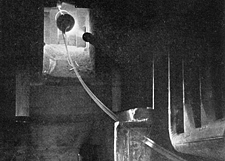 |
|
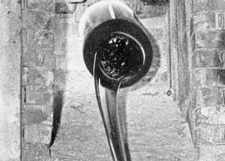 |
|
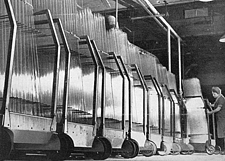 |
Glass Furnace and Control Panel (17) |
|
Danner Glass Tubing Line, 1952 (3) |
|
Detail of Danner Mandrel, 1950 (17) |
|
Stock of Fluorescent Tubing, 1950 (17) |
|
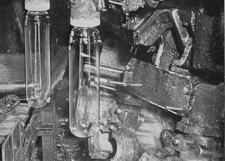 |
|
 |
|
 |
|
 |
Westlake Bulb Machine, 1950 (17) |
|
Ohio Bulb Machine, 1950 (17) |
|
Ohio Bulb Machine, 1950 (17) |
|
Inspection of Blown Bulbs, 1950 (17) |
Factory Movies
|
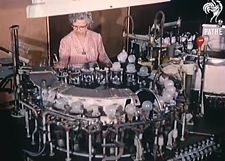 |
|
 |
|
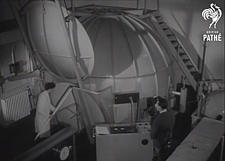 |
|
|
British Pathé visit to Osram, 1960 (18) |
|
Strike-A-Light, Open University, 1989 |
|
3m Integrating Sphere at HRC, 1952 |
|
|
Examples of Wembley Lamps
Incandescent
|
 |
|
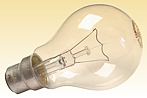 |
|
 |
|
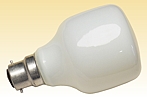 |
|
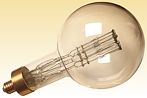 |
|
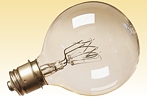 |
GLS First Coiled-Coil |
|
GLS with Single Support |
|
GLS with Plastic Cap |
|
Osram Accent Decor |
|
Lighthouse EC111 |
|
Lighthouse L/11 |
|
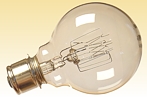 |
|
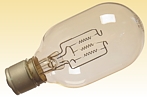 |
|
|
|
|
|
|
|
|
Lighthouse L/5 |
|
Lighthouse L/8 |
|
|
|
|
|
|
|
|
Tungsten Halogen
|
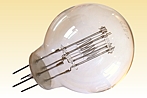 |
|
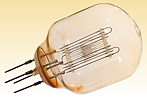 |
|
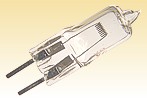 |
|
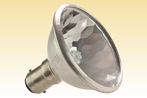 |
|
|
|
|
CP/57 Twin-Filament |
|
CP/22 Flexi-Pin Studio |
|
A1/215 Single Ended |
|
M/84 Power Beam |
|
|
|
|
Short Arc Mercury (from Hirst Research Centre)
|
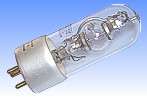 |
|
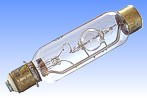 |
|
|
|
|
|
|
|
|
ME/D Short Arc 250W |
|
ME/H Short Arc 500W |
|
|
|
|
|
|
|
|
1 |
The Mass Production of Incandescent Electric Lamps, G. Chelioti, GEC Journal Vol.1 No.4 May 1931, pp.35-40. |
2 |
The GEC Research Laboratories 1919-1984, Sir Robert Clayton & Joan Algar, Peregrinus Ltd., ISBN 0 86341 146 0. |
3 |
Osram Lamps In the Making, 1952. |
4 |
The History of the Tungsten Filament Lamp, J.A. Moore, GEC Journal Vol.25 No.4 October 1958 pp.1-15. |
5 |
Lamp Making, E.F. Edwards & L.G. Timmins, Light & Lighting Journal (UK) Nov/Dec 1974 pp. 254-265. |
6 |
Machines for Electric Lamp Manufacture, H.W.B. Gardiner, E.A. Heywood, W.J. Wordsell, Meeting of the Instition of Mechanical Engineers, 6th March 1963. |
7 |
Death of a Lightbulb, J. Otten, Blue Ocean Publishing 2012, p.213. |
8 |
Private Communication, Graham Skeldon - Osram Wembley, 1995. |
9 |
Private Communication, Ray Burgin - ex-Osram Wembley, 1998 and 2015. |
10 |
Private Communication, Ken Foreman - ex-Osram Wembley, 2012-2014. |
11 |
The Osram-GEC Photo Archive, Tim Newberry. |
12 |
Historic Photographs of Osram-GEC in England, John Reeves. |
13 |
Britain From Above 1919-1953. |
14 |
Osram-GEC Lamp Catalogue, 1932. |
15 |
Osram-GEC Lamp Catalogue, 1937. |
16 |
Osram-GEC Lamp Catalogue, 1951. |
17 |
Osram-GEC Glass Works Catalogue, 1950. |
18 |
British Pathé - Historic films of Osram. |
19 |
Photo taken from Nitrogen Capture, Chapter 6 - The Direct Synthesis of Ammonia, A.S. Travis, publ. Springer AG, 2018, p.106. |
|
|
|
|
|
|