|
|
Introduction
Following Dr. William Coolidge's 1909 invention of the drawn tungsten wire process at GE's Schenectady Laboratories, the Cleveland Wire Works was established in 1913 to take over its production on an industrial scale. The plant's activities commenced with the extraction of tungsten metal from the oxide, its purification, sintering into bars, followed by swaging and drawing into wire. Because of its metallurgical similarities molybdenum wire was also produced, along with solid refractory metal parts such as tungsten anodes for X-Ray tubes, and superhard tungsten-based alloys for industrial tooling. Despite its name, the site also produced Argon gas until 1972, by which time it had become more readily available and could be obtained from standard gas suppliers.
|
Aerial View of the Cleveland Wire Plant, approx. 1960s3
|
Address |
GE Tungsten Products Plant #7641, 21800 Tungsten Road (formerly 1331 Chardon Road), Euclid, Ohio 44117, U.S.A. |
Location |
41.5772°N, -81.5339°E |
Opened |
1913. |
Closed |
26th March 2010. |
Products |
Tungsten and Molybdenum wire and their chemical precursors, formed and sintered refractory metals, cemented carbides, argon gas. |
Tungsten Wire
The Cleveland Wire Division of General Electric was established in 1913, as the world's first dedicated site for the mass production of drawn tungsten wire. This activity was taken over from the company's central laboratories at Schenectady, where the process has been invented a few years earlier on a small lab scale. The production operations were vertically integrated right back to the processing of the raw tungsten ore, and are summarised in an article by G.A. Barker who visited the factory for the February 1925 issue of the GE Magazine of Light:
The black ore from the mines, containing tungsten in its natural state, is first ground to the fineness of talcum powder. This powder is treated with boiling lye in an 'ore digester' in which it is agitated by wooden paddles until thoroghly dissolved, forming sodium tungstate. It then goes through a series of ten successive reactions with various chemicals in large tanks and vats, it is 'doped' with certain materials, and finally (as modified tungstic oxide) reduced to the form of black metallic tungsten by heat in a special furnace.
The exact nature of the chemical processes and the exact nature of the 'materials' introduced will depend on just what the wire is to be used for - each has a specific purpose in improving the final quality of the lamp. Wire for vacuum (Mazda B) lamps is made by a very different formula than wire for gas-filled (Mazda C) lamps.
The black tungsten powder is bolted through silk cloth, then formed (dry) under tremendous pressure into an ingot that looks something like a piece of gray, square, narrow picture moulding, a foot or two long. Then it is baked in an electric furnace. After this baking it is strong enough to be picked up in the hands without danger of breaking. It is then 'sintered' by passing a heavy current through it (all of this heating must be done in an atmosphere of hydrogen), and is now ready for swaging. After receiving many millions of blows in some thirty successive swaging dies, our ingot has become a round wire about 1/32 inch thick and about seventy-five feet long. It is then ready for drawing through the diamond dies. The wire, before it goes through each die, passes through a lubricating solution and then over a fire which bakes on the lubricant and softens the wire for drawing. A single ingot may yield as much as one hundred miles of filament wire, which, in its final form, is worth many times its weight in pure gold.
This, briefly, is the 'ordeal of fire and water' that results in tungsten wire for lampmaking.
In 1955 the plant was strengthened with the opening of the Refractory Metals Laboratory, which took over the research activities of Schenectady and further accelerated technical progress by bringing both production and development onto the same site. For many decades the Cleveland Wire Plant, later known as the Tungsten Products Plant, was the worlds largest producer of tungsten as well as molybdenum. Besides the lamp industry, its high performance materials experienced widespread growth in radio and television tubes, x-ray tubes, engine ignition systems, electrolytic capacitors, swisches, thermostats and relays, and a broad variety of components for the American space and missile programs
|
Tungsten Carbide Alloys
Another important spinoff of the Cleveland Wire Works was in the development and production of cemented tungsten carbide tooling materials. This activity was triggered during the first world war, when the price of diamonds escalated considerably. Diamond was and still remains an essential component in the manufacture of tungsten incandescent lamps, because of its use in the manufacture of wire-drawing dies. Tungsten is so hard a material that only natural diamond is sufficiently strong for making the dies used to draw it to the fine diameters required for lamp filaments.
Owing to the inflated price of diamonds, GE began a research program to develop alternative materials at the Edison Lamp Works in Harrison NJ, and at the Cleveland Wire Works. A similar effort was initiated by the Osram lamp company in Berlin, and the Germans ultimately achieved a superior material consisting of tungsten carbide particles cemented together with metallic cobalt. The Osram material was named Widia, an acronym of the German "wie diamant", or in English "like diamond". Both materials were suitable for drawing tungsten wire to all but the smallest diameters (for which natural diamonds still remain the sole option) but the Osram Widia had the additional advantage of being supremely suitable for the manufacture of hard tool materials for all kinds of metalworking.
Osram was of course only interested in its new material because of its importance in lamp manufacturing, and for the industrial tooling applications it licensed the use of this material to the Krupp steel company. Because of the international patent agreements between GE and Osram, and indeed most of the worlds principal lampmakers at that time, GE automatically had the rights to produce and use Widia in its own lamp factories. However GE had considerably broader business activities than Osram, and recognised the importance of tungsten carbide tooling materials for the rest of its business operations. In 1928 GE indirectly obtained the rights to the use of the Osram material for all applications, via another patent agreement signed with Krupp. From that time onwards the Cleveland Wire Works grew to considerable importance as a leader in the American business of cemented carbide materials, a position which General Electric maintaned for almost a century. Its 'Carboloy' materials were considerably improved over the following decades, and its leading position ultimately enabled GE to obtain the business of other major corporations such as the Ford Motor Company, for their hard tooling and cutting materials.
|
Argon
Following the invention of the gas-filled incandescent lamp by Dr. Irving Langmuir of GE's Schenectady research laboratories, the world's first large-scale industrial application for argon gas was realised. At that time the entire global capacity for the production of argon did not meet the requirements of the lamp industry, and moreover the traditional suppliers could not deliver suitably pure gas. Like most of the world's principal lampmakers, GE therefore established its own laboratory-scale production of argon. Crude argon was at first purchased from the Linde gas company, and starting in the autumn of 1914 the GE research labs were able to remove sufficient of the nitrogen and oxygen that a small quantity could be tested at the Lamp Development Laboratory of Nela Park. By February 1915 production was commenced and argon cylinders were delivered to the lamp factories, which were enabled to introduce new lower wattage and more efficient incandescent lamps. Demand continued to escalate, and in 1919 the National Electric Lamp Works of GE established its own complete argon distillation and purification facilities within the Euclid Lamp Plant.
Thereafter, the production of argon gas was adjoined to GE's Refractory Metals Division, and production was absorbed into the Tungsten plant. This remained one of the core activities of the site until 1972, by which time other applications for argon had been developed and gas of sufficiently high quality could be purchased from the standard producers of industrial gases.
|
Factory Movies
|
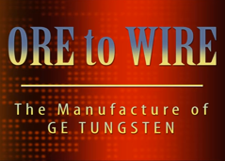 |
|
|
|
|
|
|
GE Promotional Film, 1964(4) |
|
|
|
|
|
|
References & Bibliography
- A Century of Light, James A. Cox, published by The Benjamin Company / Rutgers, 1979, ISBN 0-87502-062-3, p.153.
- Hearings Before the Committee on Patents, United States Senate, 77th Congress, 2nd Session, Part 1, April 13-17 1942, pp.252-255.
- Factory photos provided by Edmund Tobin (former employee of 38 years).
- Factory video provided by Edmund Tobin (former employee of 38 years), July 2021.
|
|
|
|
|