|
Merthyr Tydfil - Swansea Road |
|
Introduction
The Thorn Lighting works in Merthyr Tydfil was the second largest employer in this Welsh mining town, at the peak of its operations employing around 1500 people in the manufacture of incandescent lamps and filaments. Merthyr was a high volume factory producing many millions of lamps per week and for many years was the most efficient incandescent lamp factory in the whole of Europe, but it was closed in 1992 shortly following the takeover of Thorn by GE Lighting of America. GE only wished to keep the three highest speed lines and abandon the rest of the production. Such a large factory building was no longer required, so the fast lines were transferred to Leicester, and the rest of the factory closed.
|
Bill Keating, former plant foreman at rear of Thorn Lighting Merthyr Tydfil, 1993
|
Address |
Swansea Road, Merthyr Tydfil, South Wales, United Kingdom. |
Location |
51.7507°N , -3.3913°E |
Opened |
1947 |
Closed |
1992 September |
Products |
Incandescent GLS, High Watts, Coloured, Crown Silver, Blown Reflector, GLS and Halogen Filaments, Fluorescent Cathodes. |
Swansea Road Works
The Merthyr Tydfil factory was built in 1947 to satisfy the rapid expansion of Thorn Lighting's original lampmaking subsidiary, Atlas Lighting. That company had originally established its manufacturing at premises in Edmonton, North London, but after ten years of operations it became clear that larger premises would be necessary to meet the growing demand. The mining town of Merthyr Tydfil in the Swansea Valley was no doubt chosen on account of the copious availability of technically skilled and low cost labour in the area, combined with the fact that financial support was available from the local government for the creation of high quality jobs.
Within a year of its opening, Jules Thorn had signed a technical agreement with Sylvania of America for co-operation on development of lamps as well as manufacturing equipment and right from the outset, Merthyr benefitted from access to the high speed equipment designs that were being pioneered in America. These were able to produce lamps much more quickly and with lower costs than the traditional lampmaking machinery in use at the time in Europe.
A further expansion came in 1965 when Thorn decided to build three new machines according to the unique Sylvania "Dual head" concept, in which two lamps instead of one are produced with each index of the rotating machinery. At that time the fastest machinery in Europe was running at a speed of about 2000 lamps per hour, but the Dual machines at once increased this output to an impressive 3600 lamps per hour - one per second. The new machinery was built at Thorn's own equipment works in Enfield and was trialled there for a number of years, before being transferred to Merthyr to capitalise on that factory's low labour costs.
|
Goat Mill Road Works
The rapid increase in lamp production at Merthyr brought with it a similar increased requirement in raw materials. At the time of the factory's foundation, Thorn only produced its own metal caps via its subsidiary factory, Lamp Presscaps Ltd, which continued to operate in the Edmonton factory from which Merthyr had been founded. Other key components such as glass bulbs, glass tubing, leading-in wires and tungsten wire were purchased from the joint AEI-GEC companies Glass Bulbs Ltd, Glass Tubes & Components Ltd, and Lamp Metals Ltd. However the production of the coiled tungsten filaments, a particularly expensive component and one which determines in great measure the performance and quality of the lamp, is one part that Thorn wished to control itself.
A secondary factory was established in Merthyr on Goat Mill Road and this was concerned with the production of tungsten coils. Braided, Triple Coil and Stick cathodes were also made, for use in the company's fluorescent tubes made at Enfield.
Coiling machinery was also designed and built in the Equipment Works at Merthyr, and a particularly important development allowed Thorn to dramatically reduce the cost of its coiled-coil filaments. Traditionally filaments are wound on a mandrel wire, made of molybdenum, which is used to set the diameter of the coil and keep its shape correct while it is furnaced to develop the necessary grain structure in the tungsten wire. After stabilising, the mandrels are dissolved out by immersing the coiled filaments in a concentrated mixture of nitrosulphuric acid. In the 1980s Thorn was the first to avoid this costly and wasteful step with the development of its retractable mandrel machinery. In this process the tungsten wire is first coiled around a fixed mandrel to form the primary coil, then coiled around a hardened steel pin to form the secondary coils. The pin is withdrawn from the secondary coil after winding, and allows a significant increase in production rate while also avoiding the wastage of dissolving out a heavy-guage molybdenum wire as had previously been necessary for the secondary coils.
|
Transition from Thorn to GE Lighting
In the years following Sir Jules Thorn’s death in 1980, the importance of his personal involvement in the company’s success became apparent. He had built a management team comprising a large proportion of technical men, many of whom had cut their teeth at the front line of lamp or luminaire design and manufacturing, as well as others having a sharp knowledge of lighting design and applications. After his death and particularly following the merger with EMI Records to create Thorn Electrical & Musical Industries, the senior management positions were progressively filled by staff having financial and commercial backgrounds, frequently with no prior involvement in the lighting industry. The lack of direction and investment from the top had a profound effect on the company’s fortunes and within a decade the once phenomenal profit margins were giving way to a struggling company on the verge of bankrupty. The Lamps group in particular suffered strongly, being a business which has always relied on advanced new technologies. There was increased competition from continenatal and American firms who enjoyed global markets and made major invesments in lamp research, which could not be matched by Thorn's sales revenues that were built largely on its sales from the UK market alone. Despite being the clear market leader in UK, Thorn's position globally was much less significant. The reduced flow of innovations transformed Thorn into a company better known for its commodity products, whereas the high-tech new lamps which earned considerably greater margins were increasingly being specified from its foreign competitors.
The management of Thorn EMI eventually realised that its Light Sources operation was too small to compete alone in the newly globalised markets, and decided to exit the business. It came very close to being purchased by GTE Sylvania of America, with whom Thorn had enjoyed a close technical and patent interchange agreement since 1948 for the design and development of lamps and manufacturing equipment. However GTE itself then decided to put its subsidiary Sylvania up for sale, so as to fund its own transition from land-based to mobile telecommunications, and any possible takeover of another lampmaker was then off the agenda.
Meanwhile GE of America had become a company with its focus almost entirely on the American market since the international antitrust and cartel laws established after WW2 had stripped it of its controlling interests in all of the major European and Asian lampmakers. It was also in need of once again building a global presence, and had been in negotiations to re-acquire its control of Tungsram of Hungary, the dominant force in lighting for Eastern Europe. Tungsram however had no significant presence in either the UK or the former colonies where Thorn was strong, and GE’s management was quick to recognise the strength of adding Thorn to its portfolio. The Leicester and Enfield sites in particular still employed a strong arsenal of light source engineers, and thanks to Thorn's long-standing technical links with Sylvania on machine design, the company had some of the fastest and most efficient manufacturing equipment in Europe for the production of commodity light sources. Thorn also owned jointly with Sylvania a strategically important factory in Italy having state of the art production facilities for incandescent lamps, as well as other jointly owned lamp factories in Australia, New Zealand and South Africa – all territories where neither GE nor Tungsram had an interesting market share. It was felt that under the correct management of GE, whose ambitions were clearly still focussed on excellence in lamp research and manufacturing, Thorn could be put back on track and resume its once profitable position.
A deal was swiftly reached, which led to the formation of the transitionary company GE-Thorn Lamps Ltd in February 1990, under which GE took over the light source interests of Thorn Lighting. The luminaires and control gear divisions remained with Thorn. The lamp factories at Leicester and Enfield were transferred to GE-Thorn, while those at Merthyr Tydfil, Preston Kent Street and Rodney Place (Wimbledon) remained under the ownership of Thorn but managed by GE-Thorn with the intention that they would be closed at the earliest convenience. By July 1992 the integration process had been completed, and GE-Thorn was transformed into GE Lighting Ltd.
|
The GE-Thorn Era
Much of the Merthyr production was duplicated elsewhere in Tungsram, and the labour costs in Hungary were at the time significantly lower than in Britain. GE therefore had to make difficult decisions concerning which parts of the Thorn manufacturing should continue. It was eventually decided to retain only the three high speed "Phase 3" lines from Merthyr, which since their introduction had been pushed up to manufacturing speeds in excess of 5000 lamps per hour. It was felt that their high speed would counteract the costs of British labour and make continued production of standard GLS lamps possible in the country.
However the Merthyr site was too large to be used for running just these three lines, so it was decided that it would be most economical to close that site and transfer those lines to the GE-Thorn factory at Leicester. By this time, the Phase 3 machines were approaching 30 years of age, and in need of renovation to ensure their continued high efficiency production. It was planned to remove one line at a time, return it to the Enfield Equipment works which had originally built the machinery for a full renovation, and then relocate it to the Leicester factory for continued production. Lines C and B were successfully relocated, and the engineers at Leicester succeeded in driving manufacturing speeds still higher, to well above 6000 lamps per hour. However to compete on a global scale in incandescent manufacturing, cost pressures are immense. Despite the slower machinery in Hungary and Italy, those countries' lower labour rates ensured that they always had the edge on cost. It proved impossible to achieve a speed-scrap compromise which could compete with the lower labour costs in Hungary and Italy, and before the third line A could be transferred to Leicester, the decision had already been made to cease incandescent lampmaking in Britain.
|
Photographs
|
 |
|
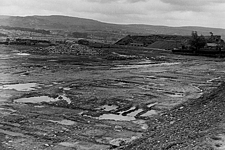 |
|
 |
|
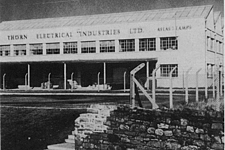 |
|
Before Construction |
|
Before Construction |
|
Construction 1947 |
|
Construction 1947 |
|
|
 |
|
 |
|
 |
|
 |
|
Coronation Decoration 1953 |
|
Factory in the 1960s |
|
GLS Department, 1960s |
|
Coiling Department, 1960s |
|
|
 |
|
 |
|
GLS Packing, 1970s |
|
Factory Demolition, 1993 |
|
Factory Movies (3)
|
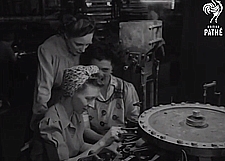 |
|
|
|
|
|
|
Merthyr Girls at Edmonton, 1946 |
|
|
|
|
|
|
|
|
|
|
|