|
|
Introduction
Hammersmith was one of the earliest lamp factories in Britain, having been set up in 1881 to manufacture the Lane-Fox type of carbon lamps. Following the closure of that company by the Ediswan litigation, it was resurrected as the Robertson Lamp Works and came under the control of the General Electric Company of England. Later it established a joint venture together with Osram of Germany to produce Tungsten lamps, and further diversified into fluorescent and discharge lamps, as well as various electronic tubes. That latter category became its main product family, with lampmaking progressively being decentralised to other new GEC factories. Hammersmith survived for well over 100 years, with production finally coming to an end in 1988.
|
General View of Hammersmith Lamp and Valve Works, Approx. 1921-23
|
Address |
Brook Green, Hammersmith, London, United Kingdom. |
Location |
51.4973°N, -0.223906°E. |
Opened |
1880, with start of incandescent lampmaking in 1881. |
Closed |
Lampmaking ended 1955/56. Demolished 1988. |
Products |
Carbon Arc, Arc Lamp Carbons, Carbon Filament Lamps, Osmium & Tungsten Filament Lamps, Tungsten Wire, Argon Gas, Linear Fluorescent, Low Pressure Sodium, Medium Pressure Mercury, High Pressure Mercury, Electronic Valves, Cathode Ray Tubes. |
Foundation by Brush
In 1879 Charles F. Brush, the American arc-lamp pioneer, sent one of his staff, Thomas Montgomery, to England with the aim of promoting overseas business for the Brush company. He established the Anglo-American Brush Electric Lighting Company, whose purpose was to exploit in Britain the American patents of Brush. Although Brush manufactured a wide variety of electrical devices, the principal product at the time was the carbon arc lamp. The Brush lamps were superior to all others, thanks to a particularly elegant invention which involved a combination of electrical and mechanical regulation to feed the carbons at the same rate as they were consumed, thereby avoiding flicker and the need for continual adjustment.
Within a year it was clear that local manufacturing of both arc lamps and carbons could be justified in England, and Montgomery succeeded in attracting £800,000 of investment from London financiers for the purpose of establishing an indepenedent arc lamp manufactory in Britain. It is not clear from the literature where this factory was located. Some references cite its location as Brook Green in Hammersmith, whereas others refer to the main Brush works at Lambeth.
Around the same time the early breakthroughs in incandescent lamps were taking place, and the company desired to expand its business into this exciting new area. Like many others, they were blocked due to strong patents held by the Edison-Swan companies. However in 1881 a new lamp was developed by St. George Lane-Fox with the intention of circumventing these patents. His invention was to avoid the use of a single metallic conductor running from the evacuated interior of the bulb all the way to the outside contact terminals, by disposing small pools of the liquid metal mercury inside the stem of the lamp. Only very short leads extended from the bulb into these mercury-filled chambers, and separate wires, also immersed in the mercury, supplied the current from outside.
Seeing this as their way into the incandescent lamp business, Anglo-American Brush leapt on the idea, bought the Lane-Fox patents for £50,000, and engaged the services of the man to set up manufacturing in a purpose-built new lamp works at Brook Green, Hammersmith. It is not clear whether or not this was an entirely new factory, or if Brook Green had indeed been the site of the earlier carbon arc operations. In 1881, the first year of operation they achieved sales of £80,000. The operation was a tremendous success, with sales leaping to £200,000 the following year. Many men who were later to become strongly influential in the later growth of the incandescent lamp business were employed in setting up the Lane-Fox lamp manufacturing at Hammersmith. Of particular interest are Charles Robertson and Gerard Philips, to whom reference will be made later in the further development of this factory site.
Shortly after the start of manufacturing, Anglo-American Brush received the perhaps inevitable news that legal proceedings had been initiated by the Edison-Swan companies for infringement of their patents, with the claim that the Lane-Fox design did not, in fact, circumvent their key claims. The case proceeded to court where in 1882 the matter was confirmed, and Brush was at once forced to close down its factory. Ownership of the Lane-Fox patents was transferred the following year to the American parent company, and Brush made no further UK ventures in incandescent lamp manufacturing. Later in 1890 the American Brush company was amalgamated with the Thomson-Houston Company of America, which itself merged with Edison General Electric in 1892 to form the present-day General Electric Company of America. The Anglo-American Brush company was not involved in the takeover, but retained the worldwide patent and sales rights to the American products in all countries of the world except the USA. It continues to operate today as a manufacturer of turbo-generators and heavy electrical equipment with production at the vast Falcon Works in Loughborough, England, which was established in 1889 after Brush had outgrown its original small works at Lambeth.
|
Transfer to Robertson and GEC
The new and virtually unused incandescent lamp works at Brook Green lay dormant for more than a decade, while the Ediswan litigations raged and that company fiercely shut down all of its British competitiors so as to gain a monopoly over the incandescent lamp business. It was known however that these patents would expire in 1893, and in the build-up to that momentous day more than a dozen companies began making preparations to attack the Ediswan business and by resume their own production in Britain. One of these was the General Electric Company of England, which purchased the redundant Brook Green works and engaged the services of its former employee Charles Robertson, who was eminently skilled to assist them in their desires.
Robertson was the son of a London Bullion dealer, educated at Merchant Taylors' School in London and won a scholarship to St. John's College Oxford, which he was most unfortunately unable to take up due to a change in his personal situation. Instead he remained at home and studied Electrical Engineering and Analytical Chemistry at Finsbury Technical College. In 1881 he joined the Anglo-American Brush Electric Light Corporation and became assistant to St. George Lane-Fox, in establishing the original incandescent manufacturing at Hammersmith. He quickly found promotion elsewhere, and became manager of the incandescent lamp department of the German firm Pilsen-Joel. In 1885 he joined Alexander Bernstein, for whom he equipped another new lamp factory in London, again following Bernstein's belief that he had developed a design that circumvented the Ediswan patents. But it was not to be, and Bernstein was also shut down by the Ediswan litigation. The Ediswan actions were quite ruthless in Great Britain. Rather than offering a license to their patents as was done by the other dominant firms around the rest of the world, Ediswan instead went for full eradication of all of its competitors, such that it could absorb their production volumes into its own factory at Ponders End.
Realising that there was no potential for a man skilled in lampmaking to find work in Great Britain, Robertson's next step saw him emigrate to the Netherlands. There he joined forces with Gerard Philips, who had also worked at the original Brush / Lane-Fox factory in Hammersmith. Philips was determined to set up his own lamp factory in his home country of Holland, which at the time had no patent laws at all. There he was free to manufacture lamps that infringed the Ediswan patents, but could of course only sell them in the Netherlands and other territories where the Ediswan companies had no protection. Philips needed technical assistance to set up the factory, and Robertson had the skills he needed. Robertson deeply wanted to form a partnership with Philips, but that idea did not fit into Gerard's plans. Philips wanted outright ownership, and offered to hire Robertson only to help him start up the production, which commenced at Eindhoven in 1891.
All of these ventures bought time for Robertson, who knew that his chance would come with the 1893 expiry of the Ediswan patents in his home country of England. During the previous years he had assisted in the establishment of numerous lamp factories for various investors, and from a study of the successes and failures of each operation, must have built up considerable expertise in how the optimum factory should be organised.
Meanwhile Hugo Hirst of the General Electric Company of England had built up a strong position in all things electrical - except of course incandescent lamps, which he had been blocked from entering due to the Ediswan monopoly. GEC made its own lighting fittings and the entire power generation and distribution equipment, and it was a natural fit to wish to be able to sell lamps along with these, and to secure a cost-effective supply of the same. Prior to the expiry of the Ediswan patents he visited many lamp factories in Germany, Austria and America where there were numerous manufacturers - the owners of the patents in those countries had taken a different strategy than Ediswan in Britain, and chose to offer licenses to the smaller producers in return for payment of a royalty on each lamp, rather than putting them out of business. Hirst met Robertson in Vienna, and the conclusion of their meeting was that the two men would establish Robertson Electric Lamps Limited, a company to be based in London and half owned by GEC and half by a group of smaller individuals. It is believed that Robertson must have also had some share himself.
The result was a particularly fruitful marriage. Robertson achieved his long-term goal of being manager of his own incandescent lamp factory, and the GEC at once became a formidable competitor of Ediswan. The new partnership was so successful that within just a few years, Robertson Electric Lamps and therefore also GEC had become the largest lamp manufacturer in Britain. In part this was fuelled not so much by their own success, but the weakness of Ediswan. During the monopoly years that company had of course no need to innovate and improve its manufacturing, because it had no competitors. Continental and American lampmaking methods had however made tremendous strides forward in production technology, and when Robertson and a dozen other small companies set up in competition against Ediswan in 1893, based on the latest developments in lamp production, they were rapidly able to erode the Ediswan market share. The Robertson Electric Lamp Company was floated on the stock market in 1901, with a value of £0.5 million.
|
Tungsten Lamps and Co-Operation with Osram
Following Ediswan's establishment of a monopoly, that company's directors decided that there was no further need to continue with expensive investments in research and development for new and better lamps. They enjoyed very satisfactory profits from making old-fashioned lamps and having the freedom to sell them at extortionate prices thanks to the total absence of any competition. As a result the monopoly years represented the darkest period in the British lighting market, and the country progressively slipped further and further behind the tremendous improvements in both lamp performance and manufacturing efficiency that were being achieved in the normal market situations elsewhere around the world.
The end of the monopoly saw a change in fortunes for many companies - namely the impressive growth of a dozen or so newcomers who had based themselves on more recent continental developments, with their gains being fuelled by the demise of Ediswan. Following the settling-down of the market, the carbon lamp had been perfected almost as far was as possible and the rate of research and development was naturally slowing down as that lamp reached full maturity. Consequently, there was still little need for establishing new light source development laboratories in Britain.
Continenal researches however did continue their investments, with the painstaking search for better filament materials than carbon. The German Auergesellschaft pioneered the Osmium filament lamp in 1902, followed swiftly by Siemens' development of the Tantalum lamp in 1905, but neither was ideal. The Osmium filaments were expensive and immensely fragile due to the process of squirting a mixture of osmium powder through a small die in an organic binder, and then sintering the resulting thread to a filament of metallic tungsten. The tantalum filaments were easier to form by standard wire-drawing processes, but could not be operated on alternating current. Both problems were solved with the invention of the Tungsten lamp in Vienna by the German/Hungarian invetor Alexander/Sándor Just, and his Croatian colleague Franjo/Franz Hanaman, who developed a process of converting a carbon filament to tungsten by heating the same in an atmosphere of tungsten oxytetrachloride and hydrogen. They licensed their process to the predecessor of the present-day Tungsram company of Budapest, who became the first manufacturer of tungsten lamps.
As soon as Hugo Hirst heard of these impressive achievements, he sent his engineers to visit the Budapest factory while he departed to meet Just and Hanaman in Vienna, making use of his own German origins to seek the rights to use their process in Britain. Before a deal was reached, Hirst heard of the developments of Auer's Welsbach company in Germany, who had improved its Osmium lamps by making a mixture of osmium and tungsten in the filament. Incidentally, Welsbach named these the OSRAM lamps, derived from the names of the two filament materials OSmium and wolfRAM (the German name for Tungsten). The situation was further complicated when patent litigation was instigated between the two competing Tungsten companies.
It was not at all clear which company would win and with whom Hirst should work, so he took the initiative of inviting both parties to London with himself acting as middleman, to determine how best all companies could capitalise on their inventions in the British markets. After a month of negotiations it was decided on October 18th 1907 to set up a new company, to be called the Wolfram Metal Filament Lamp Works Ltd, in which GEC, Auergesellschaft, and Just & Hanaman all had equal shares.
It is believed that the manufacturing at first took place within the Robertson works, in which GEC had a 50% shareholding. It was intended to manufacture both Osmium and Osram lamps according to the Auer process, and Tungsten lamps according to the Just & Hanaman process. While Hirst was waiting for production to begin, he ordered one million Osram lamps from the Auergesellschaft in Berlin. Many people thought him insane to make such a massive investment in a new product, but following the first ever newspaper advertising campaign for an electrical product, he achieved tremendous success and the lamps were sold far more quickly than had been expected. This gave added impetus to ramp up the manufacturing as quickly as possible, after which it soon became obvious that the Auer process was superior. Manufacturing of the Just & Hanaman style lamps was abandoned, and that partner sold its shareholding, which saw ownership of the Wolfram works being split equally between GEC and Auergesellschaft. In 1908, the German Auergesellschaft transferred the rights to its Osram brand name to Wolfram Metal Filament Lamp Works, for us in the United Kingdom and all of its colonies around the world. The following year in 1909 production was transferred into a purpose-built new Tungsten Lamp Factory alongside the original Brush/Robertson Carbon Lamp Works, and in 1910 the name of the operation was changed to The OSRAM Lamp Works Ltd.
|
Full Ownership by GEC
A third lamp-related factory entered the GEC portfolio in 1908, when to fuel the rapidly increasing demand for electric lamps, Robertson acquired a glassworks at Lemington-upon-Tyne in the North of England. In a step towards amalgamation, the Osram Lamp Works purchased the Robertson Lamp Works and its subsidiary glass factory in 1914, to form the new Osram-Robertson Lamp Works Ltd. This company automatically became owner of the OSRAM brand name throughout Britain and the colonies.
Following the outbreak of the first world war, the company's fortunes took a sharp downward turn. The fact that it was 50% owned by a German enterprise was deeply unpopular with customers, many of whom switched to buying lamps from British competitors. As the inensity of the war heightened, a solution to its troubles was found when all German assets were seized by the Government - and in 1916 Hugo Hirst was able to buy out the former share of Auergesellschaft from the Custodian of Enemy Property for £260,000 - a momentous step which severed the German Osram company from the ownership of its brand and factories in Britain and the Colonies. A similar situation was played out in many other countries of the world, which proved catastrophic for the fortunes of the original German Osram company.
The GEC's early entry into the Tungsten lamp business along with ownership of the British rights to the tungsten lamp manufacturing process put it on a sound footing for future expansion. For a moment in 1916, its position was threatened when an importing company, G.M. Boddye & Co., began importing Dutch-made Philips lamps into Britain which of course infringed the GEC patents it had acquired. Out of court, Philips and Boddye took licenses from GEC and agreed to limit the quantity of lamps that could be imported from overseas - the balance of Boddye's requirements being supplied either directly from GEC, or not at all. This wa a model that GEC practiced on other companies as well, requiring them to pay a royalty rather than forcing them out of business as Ediswan had done earlier in the enforcement of its carbon lamp patents. The resulting mild competition that resulted was instrumental in ending the technical stagnation of the British lamp industry that had occurred under the Ediswan monopoly years and re-established Britain as a technlogical leader in subsequent lamp developments.
The shareholding of the new entirely British Osram company still did not lie 100% with GEC. When the Robertson company had been founded, GEC was only a 50% shareholder, the balance being taken up by a number of small investors. In 1917 GEC therefore arranged a bank loan to enable it to buy out the other shareholders one-by-one, a process which was completed in 1919 when the company finally fell 100% into the ownership of the GEC and its name was changed accordingly. Lamps continued however to be branded Osram in the case of Tungsten filament types, and Robertson in case of Carbon filament types.
In 1920, a famous building addition was made to the Hammersmith works. An elegant dome was built on the roof, bearing a large golden sign "Osram Lamps". Today this is the only remaining part of the factory which still stands. The workforce had already risen to an impressive total, with some 2100 people being employed in 1922.
|
The Research Laboratories
To fuel the company's further growth, Hirst recognised that investment in lamp research and continual manufacturing improvements would be essential. Prior to the 1914 war it had relied entirely on German science and technology, the withdrawal of which was a significant blow to the company. Hirst resolved never again to let his company rely on foreign technology, and set about forming his own research laboratories - not only to provide support to the lampworks at Hammersmith and the Glassworks at Lemington, but for all of the company's other electrical divisions as well.
He recruited Sir Clifford Paterson who had previously been in charge of the light measurement sectoion of the National Physical Laboratory, and in 1919 the initial laboratories were set up within a wooden hut at the Hammersmith lampworks which had been hastily erected during the war to provide extra space for making valves. It was never the intention that the laboratories should share factory space and their establishment within the works was only for reasons of speed, to allow research to begin immediately while the new site was being designed and built. That was completed in 1922 with the relocation to a new greenfield site originally intended for housing, alongside the new Osram Glassworks on East Lane, Wembley. It formed Britain's first dedicated industrial research laboratory, and was in 1961 re-named The Hirst Research Centre.
Many of the new lighting-related concepts devised here were swiflty implemented in production at Hammersmith and for decades to come it ensured that the GEC lampworks was kept brimming with new developments - especially in the field of fluorescent and discharge lamps, as well as the allied field of radio valves and cathode ray tubes which soon augmented the lampmaking at Hammersmith.
|
The Gas Plant
Immediately following the development of the gas-filled incandescent lamp by GE of America in 1913, GEC acquired rights to GE's development and set about making the higher wattage nitrogen-filled lamps. Its entry into the market for lower wattage gas-filled lamps was hindered by limitations in the availability of argon gas - this being required for the smaller size lamps which would be too inefficient if filled with nitrogen. Until this time argon had no commercial applications, and it was difficut to procure. GEC made repeated attempts to develop a British manufacturer of the gas, but it was not successful. Meanwhile, Philips had developed a highly efficient argon distillation technique and set up its own plant at Eindhoven. This enabled it to take an early and powerful position in the European gas-filled lamp market. Numerous attempts were made by the British and other lampmakers to either secure a source of gas supply from Philips or to license the essential features of its distillation plant, but for obvious reasons Philips was reluctant to co-operate.
Eventually the British Board of Trade negotiated on behalf of the UK lampmakers, and succeeded in arranging for the purchase of the necessary argon distillation plant which Philips would build, and ship to England for operation within the Hammersmith lampworks. In return, Hammersmith was required to make the gas available to all other British customers, but most painful of all, the deal also required that the British lampmakers should jointly purchase a large share of their requirement for finished gas-filled lamps from the Philips lamp factories in Eindhoven. Philips then practised a policy of procrastination in the delivery of the promised argon plant, and the numerous delays saw the British manufacturers being forced to purchase ever-greater quantities of gas-filled lamps from Eindhoven. It was not until 1920/21 that the new plant entered operation, and Osram as well as the other British lampmakers could ramp-up their own production of the smaller size gas-filled lamps. Naturally, since Nitrogen was a by-product of the new process, production of that gas was also taken up at the same time.
|
Decentralisation of Lampmaking and Closure
In particular while the Valve and Cathode Ray Tube divisions of the M-O Valve company grew, the amount of space that could be devoted to lampmaking came under pressure. The location near to the centre of London also limited the potential for building expansions. On top of this, developments in lampmaking processes began to see a greater and greater degree of mechanisation to replace the original hand labour. Whereas most factories started out with separate departments for each assembly step, modern principles favoured a straight line production layout with each line including all of the necessary processes to make a complete lamp from start to finish. The various lampmaking machines were one by one linked together and oriented in a straight line such that materials would flow in along the line, and finished lamps emerge from one end. The architectural design of the old Hammersmith works was not ideally suited to such arrangements, and combined with the requirements for more space, a decision was made to build a dedicated new lamp factory to house the new straight-line automatic production groups. This saw the opening of the GEC's Wembley Lampworks in 1930, and with it the loss of the bulk of Hammersmith's lampmaking volume - which of course was soon taken over by the requirements of the Valve and CRT divisions
During the Second World War, for safety reasons it was needed to relocate some of the most critical manufacturing away from the South-East of England where the factories were at considerable risk of being bombed. Many Valves and CRTs were shifted to a new shadow factory at Shaw for the duration of the war, but when it was safe for production to revert to Hammersmith, the space had been taken up by the introduction of another new lamp that had been developed at the Hirst Research Centre - the Fluorescent Tube. It was decided that to make room for the return of Valves and CRTs, the new fluorescent operations should be shifted out to Shaw. That left behind only the sodium and mercury discharge lamps at Hammersmith, as well as some special incandescent types. To allow Hammersmith to concentrate solely on vacuum electronic tubes, the discharge lamps were next to be relocated to Shaw, along with vacuum incandescent and some automotive lamps. The remaining incandescent lamps such as telephone indicators, high wattage and candle types were eventually shifted to another new GEC factory, at Team Valley from 1954.
Lampmaking came to a close at Hammersmith in 1955/56, survived only by the argon distillation plant, and of course electronic valves. Argon production was finally given up in the late 1970s, by which time the British Oxygen Company, the country's primary supplier of industrial gases, was becoming increasingly skilled in its own extraction of argon gas. Valve production remarkably continued until 1988, by which time the vast majority of the Hammersmith products had been replaced by modern semiconductor devices. The factory was then closed, and demolished around 1995. Only the seven-storey tower supporting the famous Osram Dome was saved, and continues to be a famous local landmark.
|
Photographs
|
 |
|
 |
|
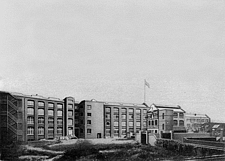 |
|
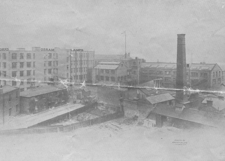 |
Original Robertson Works 1893 (1) |
|
Robertson Works and Staff, 1903 (2) |
|
Enlarged Robertson Works 1905 (1) |
|
Wolfram-Robertson Works 1910 (8) |
|
 |
|
 |
|
 |
|
 |
Osram-Robertson Works 1915 (5) |
|
Osram-Robertson Works 1919 |
|
Osram & Marconi Works c.1921-23 (1) |
|
View after final expansion, 1931 (9) |
|
 |
|
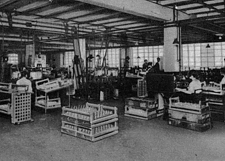 |
|
 |
|
 |
Aerial View, 1921 (10) |
|
View of one of the Sections, c.1923 (1) |
|
View of the Surviving Dome |
|
View of the Surviving Dome |
Photographs - Carbon Lamp Manufacturing, 1903 (2)
|
 |
|
 |
|
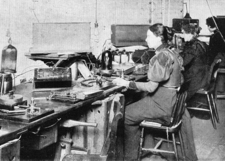 |
|
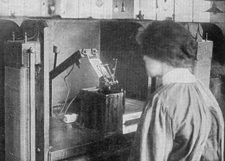 |
Carbon Filament Squirting |
|
Flashing in Hydrocarbon Gas |
|
Filament Resistance Testing |
|
Carbon Deposition on Platinum Joint |
|
 |
|
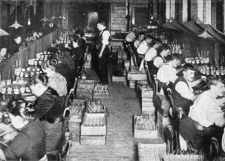 |
|
 |
|
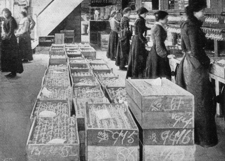 |
Tubulating the Bulb |
|
Bulb Sealing Section |
|
Lamp Exhausting Section |
|
Ageing at 150% Overcurrent |
|
 |
|
 |
|
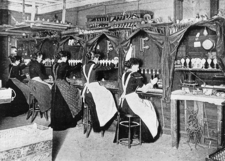 |
|
|
Frosting the Bulbs |
|
Photometry and Grading |
|
Final Inspection before Packing |
|
|
Photographs - Tungsten Lamp Manufacturing, c.1923 (1)
|
 |
|
 |
|
 |
|
 |
Tungsten Ore Baking |
|
Tungsten Rod Swaging |
|
Tungsten Wire Drawing Section |
|
Tungsten Wire Weight Gauging |
|
 |
|
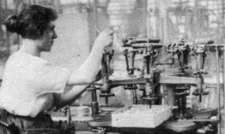 |
|
 |
|
 |
Glass Flanging Machines |
|
Foot Assembly Pinch Machine |
|
Filament Support Inserting - Vacuum |
|
Filament Mounting - Vacuum |
|
 |
|
 |
|
 |
|
 |
Filament Mounting - Gasfilled |
|
Clamping the Filament Tails |
|
Mounting - Valve Department |
|
Bulb Sealing Machine |
|
 |
|
 |
|
 |
|
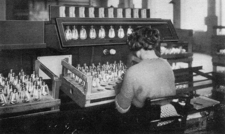 |
Lamp Exhausting Machine |
|
Lamp Capping Machine |
|
Photometry and Gauging |
|
Final Inspection and Test |
Factory Movies (11)
|
 |
|
 |
|
 |
|
 |
Hammersmith Factory 1914-18 |
|
Lamp Exhausting Section 1914-18 |
|
Tungsten Lamp Production 1914-18 |
|
Tungsten Lamp Production 1910-20 |
|
 |
|
 |
|
 |
|
 |
Tungsten Lamp Photometry 1914-18 |
|
Lamp Delivery by Horse 1914-1918 |
|
Factory Workers Leaving 1914-1918 |
|
Various Factory Staff 1914-1918 |
|
 |
|
|
|
|
|
|
Fire Evacuation Drill 1914-18 |
|
|
|
|
|
|
Examples of Hammersmith Lamps
Carbon Filament
|
 |
|
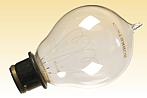 |
|
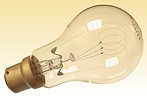 |
|
 |
|
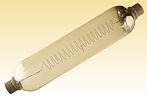 |
|
|
Lane-Fox Lamp of 1882 |
|
Early Vitrite Cap, 1901-2 |
|
Carbon Heater 65W |
|
Carbon Radiator 250W |
|
Carbon Radiator 250W |
|
|
Tungsten Filament
|
 |
|
|
|
|
|
|
|
|
|
|
Drawn Tungsten, 1911 |
|
|
|
|
|
|
|
|
|
|
Low Pressure Sodium
|
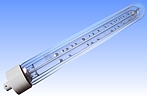 |
|
|
|
|
|
|
|
|
|
|
SO/H Dewar Jacket 140W |
|
|
|
|
|
|
|
|
|
|
High Pressure Mercury
|
 |
|
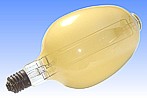 |
|
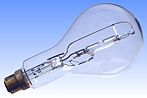 |
|
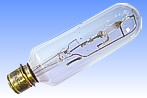 |
|
|
|
MA/V Osira 150W |
|
MAF Fluorescent 400W |
|
MB/V Osira 125W |
|
MB/D Osira 80W |
|
|
|
|
Neon Glow
|
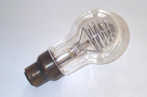 |
|
 |
|
 |
|
|
|
|
|
|
Osglim Neon Beehive |
|
Osglim Neon Letter |
|
Osglim Trolley Bus |
|
|
|
|
|
|
1 |
The Story of the Lamp, The General Electric Company of England, c. 1923. |
2 |
How The Glow Lamp is Made - A Visit to the Robertson Lamp Works, Harry Golding, The Windsor Magazine 1903 pp.638-644. |
3 |
The GEC Research Laboratories 1919-1984, Sir Robert Clayton & Joan Algar, Peregrinus Ltd., ISBN 0 86341 146 0. |
4 |
Private Communication, Graham Skeldon - Osram Wembley, 1995. |
5 |
Everything Electrical - A Brief History of GEC, Printed 1998 by the GEC Historians & Archivists Colloqium. |
6 |
Death of a Lightbulb, J. Otten, Blue Ocean Publishing 2012, pp.20,26. |
7 |
Historic Photographs of Osram-GEC in England, John Reeves. |
8 |
Osram-GEC Lamp Catalogue, 1910. |
9 |
Osram-GEC Lamp Catalogue, 1932. |
10 |
Britain From Above 1919-1953. |
11 |
British Pathé - Historic films of Osram. |
|
|
|
|
|